Stainless Steel Finishes
- Ernest D. Menold, Inc.
- Jul 3, 2014
- 2 min read
Stainless Steel is defined as an iron based alloy with a content of 0.11% to 0.30% Chromium. This chromium on the surface of stainless steel reacts with oxygen to form a thin molecular film of complex chromium oxides, which stifle corrosion.
We stock Type 304 and Type 316 stainless steel sheets in No. 2B and No. 4 finishes. For Industrial and Pharmaceutical applications, selection of the correct grade of stainless steel is essential to prevent contamination or corrosion of the product.

Type 304 stainless steel is the most widely used alloy of stainless steel in the United States. It is also known as 18-8 stainless steel due to the ratio of Chromium to Carbon (0.18% Cr to 0.08% C)
Type 316 stainless steel is chemically similar to Type 304, but it has a higher content of Nickel, and it also contains Molybdenum. The higher Nickel content provides better resistance to corrosion when in contact with chloride solutions. This better resistance to cleaning agents makes Type 316 an ideal choice for pharmaceutical applications.
When stainless steels are heated to between 800 F and 1600 F, carbide precipitation occurs. These Chromium carbides, which form on the grain boundaries of steel during welding and grinding fabrication steps, are susceptible to corrosive attack. This carbide precipitation can be reduced by using grades of stainless with lower carbon contents. Types 304L and Type 316L stainless have a Carbon content of 0.03%, which is less than the 0.08% in the Type 304 and Type 316 stainless alloys.
When the fabrication of a stainless steel part requires welding or grinding, we recommend using the "L" series of stainless if the part will be used in a corrosive environment. In pharmaceutical applications, it is common to passivate a part after welding and grinding to restore the "passive" layer of complex chromium oxides to inhibit corrosion.
Finishes
The surface finish of stainless steel is important for appearance in architectural applications, and for cleanliness in pharmaceutical and food applications. The Number finish specified corresponds to a range of machine finish for the surface. These finishes designations and what they signify are shown below:
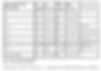
Number 4 finish is the most widely used finish for pharmaceutical applications. For some items, which are in contact with product, a mirror finish or electropolished finish might be in order.
The consideration with any of these finishes is that higher luster = higher cost, especially if welding is involved.
We can work with customers to select the right alloy, thickness and finish stainless steel to ensure that the competitively priced, fabricated product will meet their expectations in appearance and functionality.